Plywood, a versatile engineered wood product, has become an essential material across numerous industries due to its strength, durability, and cost – effectiveness. The production of plywood is a precisely coordinated process, which we’ll explore in detail with the help of visuals.
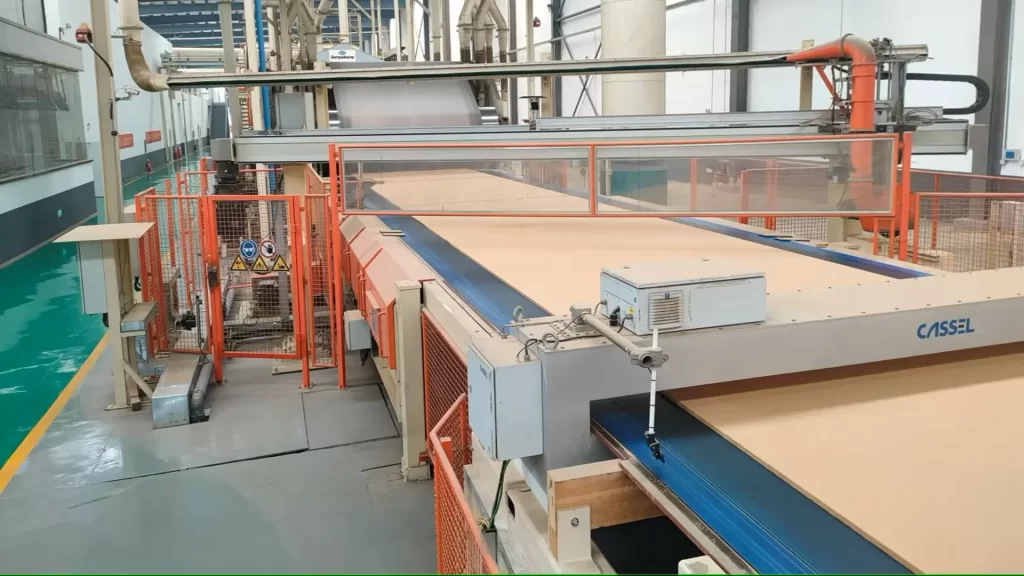
Raw Material Selection
The production of plywood commences with the careful selection of logs, the fundamental raw material. Logs are sourced from sustainably managed forests or plantations, as shown in the image below, ensuring both a continuous supply and environmental responsibility.
Ideal logs are straight, free from major defects, and of appropriate diameter, as these factors directly influence the yield and quality of the final plywood. Common tree species used for plywood production include pine, fir, oak, and birch, each offering distinct characteristics in strength, appearance, and cost. Once selected, the logs are transported to the production facility.
Debarking and Cutting
At the production facility, the first step is debarking. Specialized equipment, which may utilize high – pressure water jets or mechanical blades, removes the outer bark from the logs, as depicted in the image. This step is crucial as bark can disrupt subsequent operations and introduce impurities.
Following debarking, the logs are cut into shorter lengths, usually corresponding to standard plywood sheet sizes, using large circular saws or band saws.
Peeling into Veneer Sheets
One of the most critical steps is peeling the logs into thin veneer sheets. The log is mounted on a massive rotary lathe. As the log rotates, a long, sharp blade slices through the wood, creating continuous, thin veneer layers, as illustrated in the image. The thickness of the veneer, typically ranging from 0.2 to 5 millimeters, is precisely controlled according to the intended use of the plywood.
The quality of the veneer, including smoothness, thickness consistency, and lack of defects, is vital as it forms the basis of the plywood.
Veneer Grading and Drying
Once produced, the veneer sheets undergo a grading process. Veneers are classified based on visual appearance, strength, and the presence of defects like knots, splits, or discoloration. High – grade veneers are used for the face and back layers of plywood where appearance is important, while lower – grade ones are for the inner core layers.
After grading, the veneer sheets are dried to reduce their moisture content to an optimal level, usually between 6% and 12%. Proper drying prevents warping, delamination, and other issues in the final product.
Adhesive Application
The type of adhesive used depends on the plywood’s intended application. For exterior – grade plywood, phenol – formaldehyde resin is commonly used due to its excellent moisture resistance and bonding strength. Urea – formaldehyde resin is often applied to interior – grade plywood. The adhesive is evenly spread on the veneer sheets using rollers or sprayers, as shown in the image, ensuring full coverage.
Stacking and Pressing
After adhesive application, the veneer sheets are stacked with the wood grain of adjacent layers oriented at right angles to each other. This cross – lamination greatly enhances the plywood’s strength and dimensional stability. The stacked assembly is then placed in a hydraulic press, where high pressure and heat are applied to cure the adhesive and bond the layers firmly together.
Finishing Operations
After pressing, the plywood sheets are cooled and undergo finishing operations. Sanding is carried out to achieve a smooth surface, and the edges are trimmed to the exact dimensions, as demonstrated in the image. Additional treatments like painting, varnishing, or laminating may be applied based on customer requirements.
Quality Control
The final and crucial stage is quality control. Each sheet is inspected for parameters such as thickness consistency, flatness, strength, and defects. Non – destructive testing methods, like ultrasonic testing, may be used to detect internal flaws. Only sheets meeting strict quality standards are approved for packaging and distribution.
In conclusion, plywood production is a complex yet highly organized process that combines advanced technology and skilled craftsmanship. From log selection to the final quality – controlled product, each step plays a vital role in creating a reliable and widely used building material.